Железо по-английски
- ВКонтакте
- РћРТвЂВВВВВВВВнокласснРСвЂВВВВВВВВРєРСвЂВВВВВВВВ
- Telegram
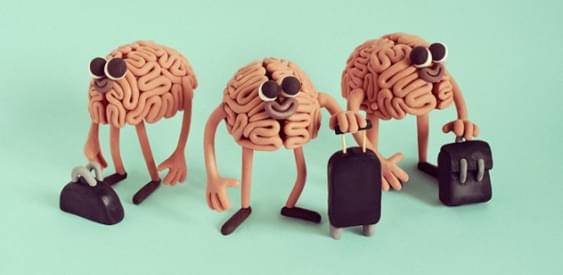
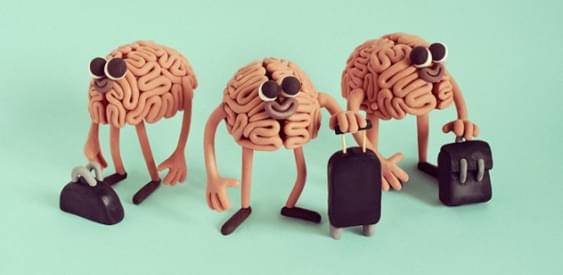
Почему красный цвет, будь то государственный флаг, болид «Феррари» или этикетка кока-колы, подсознательно вызывает чувство неуравновешенности? Возможно, дело в его стойкой ассоциации с кровью, а если быть точнее, с гемоглобином. Именно железо, входя в его состав, придает крови такой значимый цвет и попутно обеспечивает все окислительно-восстановительные реакции в организме.
Лет этому открытию, по историческим меркам, совсем немного. Можно себе представить изумление обывателей второй половины XIX века, узнавших, что между железными метеоритами (на их долю приходится всего 5 % от общего числа небесных пришельцев), компасом авантюриста-первооткрывателя и замученным рабочим-пудлинговщиком есть нечто общее! Но, как оказалось, даже в таком содержательном человеке, как, например, Бальзак, этого общего фактора – железа – хватит всего на пару сапожных гвоздей.
Тяжелая доля
Естественнонаучный прорыв второй половины XIX века позволил ответить, почему наша планета такая тяжелая. Как объяснить то, что ее средняя плотность составляет 5,5 г/см, при том что плотность самых тяжелых пород на поверхности не превышает 3,3 г/см? Очевидно, что Земля внутри совсем не однородна и устроена сложнее, чем представлялось ранее. Находки железных метеоритов в комплексе с пониманием основных принципов формирования планет Солнечной системы привели в 1866 году авторитетного французского геолога Габриэля Августа Дебре к идее о железном ядре Земли. Гипотеза эта была далеко не так сумасбродна, как могло показаться, и позволяла к тому же просто и элегантно объяснить такое загадочное явление, как геомагнетизм.
Дальше – больше. В трудах норвежца Виктора Морица Гольдшмитта, основоположника геохимии, и немецкого физика Густава Таммана (а позднее и видного сейсмолога Эмиля Вихерта) было показано, что на этапе остывания Земли происходило нечто, подобное плавке руды. Расплавленные вещества сепарировались согласно их плотности. Кора Земли образована легкими силикатами, представляющими собой банальный шлак. Ниже ушли слои штейна – смеси сульфидов и металлов, а в центральных областях сферы сконцентрировались наиболее тяжелые металлы: железо, никель и кобальт.
Как нетрудно догадаться, процентное содержание железа зависит от глубины залегания. Если ядро – практически цельножелезное (речь может идти только о разных состояниях металла, находящегося под колоссальным давлением), то в мантии его не более 13–15 %. На долю литосферы остаются сущие крохи – всего 4–5 % (здесь железо уступает первенство по распространенности алюминию). Но в общем железо можно по праву назвать «королем металлов»: оно занимает треть объема планеты, превосходя другие элементы как по массе, так и по числу атомов.
Кстати, что за странная специальность – пудлинговщик (или пудлингер)? И почему он так замучен? Основной причиной появления такой профессии стал энергетический кризис, поразивший металлургию в середине XVIII века. Индустриально развитые страны столкнулись с массовым уничтожением лесов, интенсивно пережигаемых на древесный уголь (каменный для сыродутных печей не подходил, так как содержал большое количество серы, пагубно влиявшей на качество железа). Сведение лесов порой приводило к локальным экологическим катастрофам.
Оказывается, средство борьбы с этим бедствием было известно еще в начале XVII века, и не где-нибудь, а в самом сердце Англии, в западном Мидленде. Нашел его Дад Дадли, незаконнорожденный сын лорда, который, отучившись в оксфордском колледже, приохотился к кузнечному ремеслу и очень быстро стал настоящим мастером и убежденным «гринписовцем» – жалко ему было лесов, вырубающихся ради железа. Зная проблему изнутри, юноша понимал, что в каменном угле есть какая-то вредная примесь (как мы уже знаем, это сера и фосфор), которая сильно портит выплавляемое железо и которой нет в древесном угле. Пожалуй, сложись судьба иначе, место Ньютона в истории науки было бы уже занято. Иначе и не объяснить гениальную догадку родовитого кузнеца: уголь надо прежде пережигать по образцу древесного, без доступа атмосферного кислорода (то есть подвергнуть его пиролизу, термическому разложению). Результатом стала технология выплавки железа на пережженном каменном угле (коксе), подтвержденная патентом короля Англии Якова I (который на самом деле James I) от 22 февраля 1622 года.
«Железным» магнатом Дадли не стал. Лесов в Англии еще хватало, поэтому о коксе забыли на целое столетие. Только в 1735 году на заводе Абрахама Дарби кокс занял место основного топлива в плавильных печах, подоспев ко времени очередной технологической революции, связанной с переделом чугуна.
Справедливости ради надо отметить, что пионеры металлургии шли, как говорится, ноздря в ноздрю, но в истории остались единицы. Например, близко к цели подошли братья Томас и Джордж Кранедж, предложившие перестроить печь на заводе в Коулбрукдейле в графстве Вустершир. Они переделали обычный кричный горн в отражательную печь, в которой раскаляемый пламенем свод играл роль дополнительного источника тепла. По словам управляющего, они «…построили печь такую, чтобы железо не касалось топлива, нагреваясь только сильным жаром пламени, и вскоре успех был такой блестящий, что превзошел всякое ожидание, и надо заметить, что для выделки полосового железа они брали очень твердое железо, а оно их способом делалось мягким и гибким. Я лично нахожу их изобретение необычайно важным и намерен немедленно и усердно ходатайствовать о получении патента».
Но патент судьбу братьев не изменил – они так и остались сметливыми мастеровыми с небольшого заводика. А все лавры достались бывшему морскому агенту Генри Корту. Служа по линии поставок металла, он обратил внимание на низкое качество английского железа, уступавшее шведскому и русскому. Британское адмиралтейство даже запрещало использовать его при строительстве кораблей!
Выйдя в отставку, Корт заинтересовался проблемой всерьез, полагая, что производство конкурентоспособной продукции позволит ему перехватить часть сверхприбылей экспортеров высококачественного ковкого железа. В поисках решения он объездил десятки металлургических заводов по всей Англии, вникая в тонкости производства. И прежде всего ужаснулся гигантским объемам поглощаемого металлургией древесного угля: три четверти леса, ввозимого из-за границы, идет на пережигание, оставляя другим отраслям хозяйства жалкие обрезки. Так что на каменный уголь возлагалась ответственная миссия «импортозамещения».
Чтобы проверить свои догадки, Корт арендовал кузню в окрестностях Лондона и приступил к опытам. И эксперименты увенчались успехом: в 1775 году он начинает строительство металлургического завода в Портсмуте (за счет личных сбережений). Когда встал вопрос о расширении и лоббировании в бюрократических сферах, Корт обратился за ссудой к некоему Абрахаму Джеллико, казначею Морского ведомства. И этот ушлый чиновник в конце концов лишил Корта и завода, и состояния, и патентов на изобретение. Более того, он избежал мести, благополучно отойдя на тот свет до начала расследования своих махинаций, когда выяснилось, что ссуда в 27 тысяч фунтов, выданная Корту на живодерских условиях, была украдена из казны!
Но вернемся к железу. Главная идея Генри Корта, воплощенная в 1784 году, заключалась в разделении топлива и металла: теперь в топку можно было загружать дешевый и доступный каменный уголь. Доработка печи заключалась в разделении ее объема на горновой и плавильный отделы и устройстве пода, служившего горновым сводом. Ничего сверхъестественного!
Под устраивался просто: на чугунную доску, разделявшую печь на два независимых объема (топочный и плавильный), насыпался и утрамбовывался чистый песок. Площадь пода составляла 0,5 м на центнер садки, и стандартная пудлинговая печь располагала квадратным подом 1,5 × 1,5 м с высотой свода 0,6–0,8 м. За двухчасовой рабочий цикл металлурги могли обрабатывать до 300 кг передельного чугуна.
Главная особенность пудлингового процесса – вымораживание! Хотя, казалось бы, о каком холоде можно говорить при температуре в несколько сотен градусов? Но если понимать под вымораживанием процесс кристаллизации (например, превращение переохлажденного водяного пара в льдинки), то аналогия довольно точная, с учетом того, что очищенное железо и чугун имеют разные температуры плавления (у чугуна она ниже).
Процесс начинался с подготовки пода (очистки и насыпания смеси песка с чугунной крошкой и окалиной) и предварительного прогрева печи. Чугунные чушки общей массой более 3 центнеров укладывались рядами и нагревались до плавления. И когда чугун разливался по поду слоем глубиной в дюйм, в дело вступали пудлинговщики. Длинными железными штангами-ломами они перемешивали металл с материалом пода до тех пор, пока он не начинал переходить в тестообразное состояние и свариваться в комки. Затем эти комки накатывались в крицы.
Не правда ли, «увлекательнейшее» занятие? По степени интеллектуальности напоминает подметание батальонного плаца ломами (армейское воспоминание автора). А тут еще адская жара у печей и 12-часовой рабочий день с получасовым перерывом на обед. Стоит ли удивляться, что к 30–35 годам пудлинговщики из пышущих силой здоровяков превращались в живые развалины?
Пудлингование заставляло расплавленный чугун активно реагировать с подовым материалом и очищало железо от лишнего углерода, серы и фосфора. В среднем масса крицы составляла 60–70 кг, и можно себе представить, каких усилий стоило переворачивать такой комок железа. По этому поводу известный английский металлург Д. Перси писал: «Нет производства, где бы мускульная сила человека была подвержена таким тяжелым усилиям и притом в столь изнуряющей обстановке!»
Но игра стоила свеч! В 1787 году Морское ведомство по результатам испытаний объявило, что качество сварочного железа, полученного новым методом, выше, чем у эталонного Oregrounds iron (образца из шведского Эрегрунда под Упсалой). Королевская контрольная комиссия рекомендовала применять железо Генри Корта вместо шведского для якорей и «всех железных изделий», используемых в морском деле. Содержание углерода в типичных образцах пудлингового железа не превышало 0,2 %, фосфора – 0,01, а серы оставалось всего 0,004 %. До 1 % составляли шлаковые включения, позже удаляемые в ходе проковки или вальцевания. Все остальное – чистое железо!
К началу XIX века производство пудлингового железа достигло 80 тысяч тонн (выпуск же «старого» кричного упал до 10 тысяч), причем большую часть продукции заводы поставляли в виде готового к употреблению профиля. Успехи местной металлургии позволили в 10 раз сократить импорт русского железа (в 1780-х годах это было более трех миллионов пудов). Вдохновляющий пример опоры на собственные силы!
Усовершенствованная технология быстро и надолго завоевала место под солнцем. Пудлинговое железо верой и правдой служило человечеству большую часть XIX века. Например, строительство и развитие сети железных дорог было бы просто невозможно, если бы не было дешевого высококачественного железа. К 1840 году ведущие металлургические страны: Франция, Швеция, Австрия и Россия – перешли на пудлинговый процесс, сохранив его вплоть до начала XX века. Так, в 1908 году пудлинговое железо Камско-Воткинского завода продавалось по цене 80 копеек за пуд, мартеновское – по 75 копеек, а самым дорогим было кричное, его стоимость доходила до рубля.
Однако при всех достоинствах пудлингования у него был принципиальный недостаток – невозможность получить плотную литую сталь, для этого нужна более высокая температура, чем могли обеспечить кричные и пудлинговые печи. Но это совсем другая история.
Технологии
Ким Александров