Ученые Пермского Политеха разработали способ обшивки авиадвигателя из температуроустойчивого материала
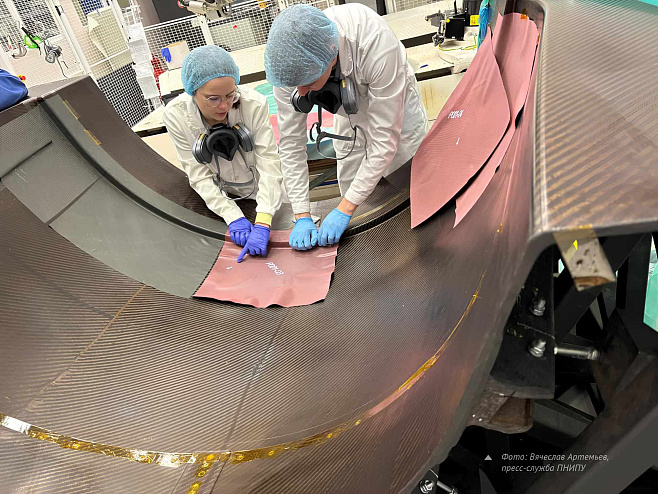
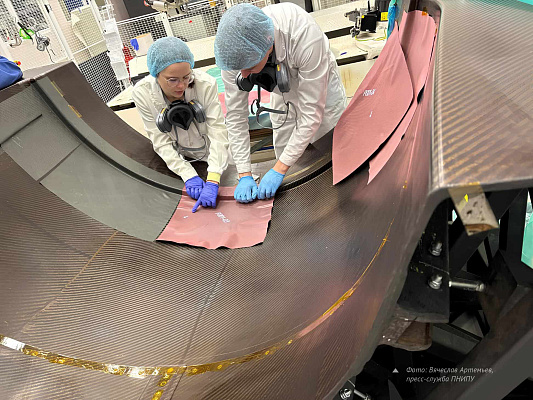
Полимерные материалы, также известные как пластики или композиты, начали активно использоваться в авиастроении с 1960-х годов из-за своих уникальных свойств. Они легче металлов, а вес – критически важный параметр в авиастроении: чем легче самолет, тем меньше топлива он потребляет, а значит сокращается объем выбросов вредных веществ. Снижение веса также позволяет увеличить количество пассажиров или грузов. Такие материалы не подвержены коррозии, обладают хорошей прочностью и жесткостью, но не все из них предназначены для работы при очень высоких температурах, какие бывают, например, в двигателях.
Ключевой частью турбореактивного двигателя, его «сердцевиной» является газогенератор. В нем происходит основное преобразование энергии топлива в энергию горячих газов. Он отвечает за создание потока газа под высоким напором и температурой, который затем используется для тяги или привода других частей двигателя. Благодаря работе компонентов этого механизма самолет поднимается в воздух. Горячие газы, выходящие из «сердца» двигателя и поступающие в турбину, могут достигать около 600-700 °C.
Различные испытания показали, что в самом газогенераторе рабочая температура повышается до более высоких значений, которые могут достигать более 800 °C, а на поверхности обшивок – до 250 °C. Поэтому возникла необходимость применять новые более термостойкие материалы.
Существуют высокотемпературные полимерные композиты, способные выдерживать до 350 °C. Их внедрение в газогенератор позволяет отказаться от тепложарозищиты, что упрощает конструкцию и снижает массу двигателя. Так он становится более легким в обслуживании и ремонте, ускоряется замена деталей.
Ученые Передовой инженерной школы Пермского Политеха разработали технологию внедрения полимеров в обшивку газогенератора. Подготовили подробные инструкции для авиастроителей, как нужно изготавливать и собирать обшивку из термостойких композитов для газогенератора, включая последовательность операций, оборудование, инструменты и материалы.
– Применение высокотемпературных полимерных композитов упрощает конструкцию газогенератора и уменьшает его массу не менее чем на 6 кг. Это облегчает сбор изделия более чем на 10%. Финалом проекта стало изготовление образца панели обшивки газогенератора в реальных размерах. Еще в ходе исследований мы подобрали оптимальный и соответствующий нормативной документации подход к проверке качества изделия. Это применение акустических методов, при которых используются звуковые волны определенной частоты для обнаружения дефектов и неоднородностей в материалах: ультразвуковой – на монолитных частях изделия, и импедансный – на участках, где пустое пространство заполнено структурой, напоминающей соты, – рассказывает Вячеслав Артемьев, заместитель директора по производству Научно-образовательного центра авиационных композитных технологий ПНИПУ.
Вячеслав Артемьев. Фото: пресс-служба ПНИПУ
Внедрение высокотемпературных полимерных композиционных материалов в конструкцию обшивки газогенератора существенно повышает эксплуатационные характеристики, обеспечивая надежность и эффективность работы двигателей. Исследование ученых Передовой инженерной школы Пермского Политеха позволит отказаться от традиционных тепловых защит, упрощает конструкцию и снижает массу воздушных судов.
Результаты исследований представлены в виде докладов на XXV-ой Всероссийской научно-технической конференции «Аэрокосмическая техника, высокие технологии и инновации – 2024» и II-ой Международной научно-практической конференции молодых ученых, аспирантов и студентов «Передовые инженерные школы: материалы, технологии, конструкции».
Технологии
ПНИПУ